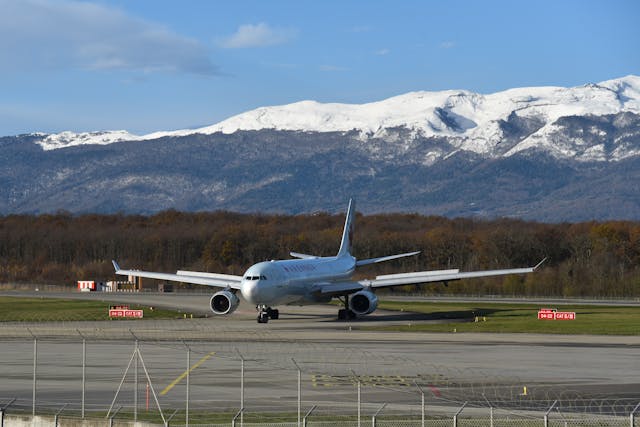
Jet engines are the backbone of modern aviation, powering everything from commercial airliners to advanced military aircraft. Developing and testing these engines requires rigorous safety measures and performance evaluations to ensure reliability. A crucial aspect of this process involves specialized testing facilities that play a vital role in ensuring the safety of jet engines.
The Purpose of Spin Pits
The spin pit is an engineered chamber designed to test the structural integrity and durability of rotating components in jet engines. These facilities subject parts like turbines, fans, and rotors to extreme speeds, simulating the intense conditions encountered during flight. Their primary goal is to evaluate how well components can withstand the forces generated by rapid spinning and identify weaknesses that could lead to failure. By replicating high-stress scenarios in a controlled setting, engineers can collect critical data about a component’s performance and durability. This testing is essential to identifying risks and ensuring the safety of jet engines under various operating conditions.
Importance of Safety in Jet Engine Testing
Safety is paramount in the aerospace sector, where even minor malfunctions can lead to serious consequences. Jet engine testing is an intensive process designed to eliminate the possibility of failure during flight. Specialized testing facilities provide a secure environment to conduct high-risk assessments.
When parts are exposed to extreme rotational speeds, they endure forces that can cause material fatigue, structural deformities, or fractures. Testing in controlled chambers helps identify such vulnerabilities early in the design phase. This allows engineers to make critical adjustments, thus minimizing the risk of in-flight issues and improving the overall reliability of the engines.
Simulating Real-World Conditions
Modern testing facilities like spin pits are equipped with advanced tools to recreate real-world conditions that jet engine components face during operation. These chambers can simulate extreme rotational speeds, elevated temperatures, and variable pressures, enabling engineers to test performance under challenging scenarios. For example, turbine blades may be spun at speeds beyond their operational limits to identify their breaking point.
Sophisticated sensors and monitoring equipment track every change in the component’s structure, providing insights into its safety margins and durability. This level of precision ensures that components are robust enough to handle demanding scenarios, such as rapid takeoffs or prolonged flights. The insights gained from testing contribute to refined designs and improved engine reliability.
Advances in Testing Technology
Over time, testing methods have evolved to incorporate cutting-edge technologies, making assessments more accurate and efficient. Modern testing chambers feature high-speed cameras, advanced sensors, and automated systems that enhance the precision of evaluations. In addition, advancements in computational modeling allow engineers to simulate how components behave under stress before physical testing begins. By combining these virtual simulations with real-world assessments, manufacturers can optimize designs more effectively while reducing development time. These technological innovations have greatly improved the safety and performance of jet engines, keeping pace with the demands of modern aviation.
Rigorous Testing for Critical Components
Vital components in jet engines, such as rotors, turbines, and compressor blades, experience significant stress due to their high rotational speeds. These parts undergo rigorous assessments to ensure they meet strict safety and durability requirements. Testing chambers subject these components to forces beyond their normal operating range, including rapid acceleration, sudden deceleration, and extreme rotational speeds. This process reveals potential failure points and highlights areas needing reinforcement or redesign. By focusing on the most critical parts, spin pits help manufacturers ensure their engines achieve exceptional levels of safety and reliability.
Improving Efficiency with Specialized Facilities
Specialized testing environments are not just about safety; they also enhance the efficiency of the development process. These facilities offer controlled and repeatable testing conditions, enabling engineers to conduct multiple assessments quickly and gather consistent data. This efficiency is particularly important for manufacturers working on advanced designs or producing engines in large volumes.
By identifying potential issues early in development, spin pits help reduce costly redesigns or recalls. Additionally, the reliability of data obtained from these tests ensures that components meet stringent performance and safety standards. This dual focus on efficiency and quality is essential to advancing jet engine technology while maintaining rigorous safety benchmarks.
Also Read: How Private Jets are Revolutionizing Executive Travel?
Specialized Engineering Solutions for Advanced Aerospace Testing
Specialized engineering services are crucial for advancing aerospace technology, particularly in designing and building custom testing facilities. These services encompass precision manufacturing, material engineering, and the creation of innovative testing chambers designed to meet the unique demands of jet engine evaluation. By applying advanced engineering expertise and cutting-edge technology, these solutions enable rigorous testing processes under realistic conditions. This ensures components meet strict safety and performance standards, making such facilities indispensable for enhancing reliability and driving innovation in modern jet engines.
A spin pit plays an essential role in the development and testing of jet engines. By providing a safe and controlled environment for high-stress testing, they ensure that components are durable, reliable, and capable of meeting the stringent requirements of the aerospace industry. As technology changes, specialized testing facilities will continue to be a vital tool in advancing aviation safety and innovation.