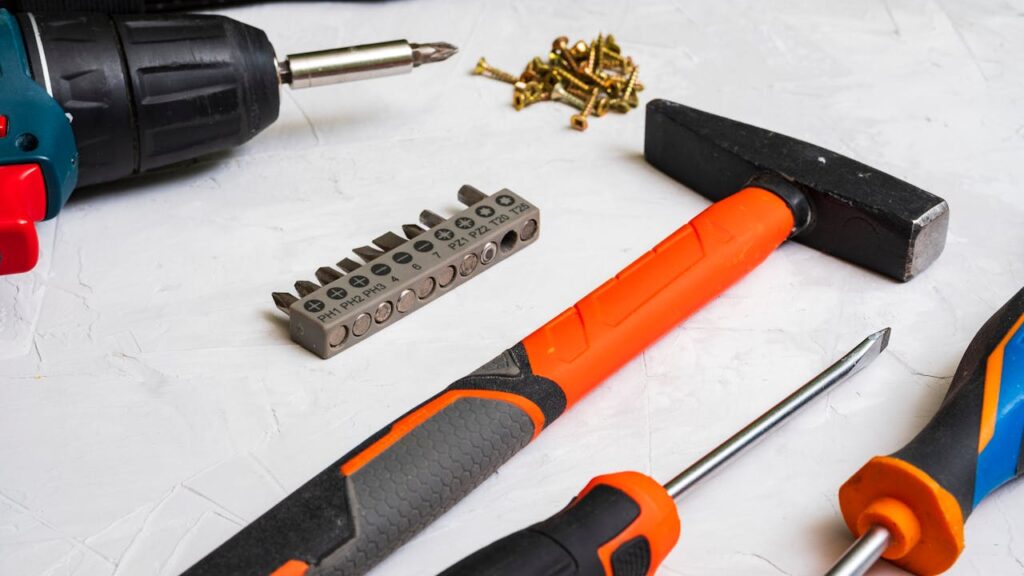
Fasteners play a crucial role in the world of industrial design. These small but essential components are the backbone of countless structures and mechanisms, providing strength and stability in everything from machinery to electronics. Understanding their importance helps users appreciate their influence on modern manufacturing and engineering. In this article, we’ll explore the role of fasteners in industrial design, from their functionality to their impact on product durability.
What Are These Essential Fasteners?
Fasteners or machine head screws are specifically designed to work with nuts or tapped holes. Unlike wood or drywall screws, they are employed in precise applications, often in metal or durable synthetic materials. The term “machine head” refers to the specific shape of the fastener’s head, which varies depending on the application.
The most common types of heads are flat, pan, and hex. Each design serves a unique purpose, allowing the fastener to provide maximum torque, grip, or flush fitting in different contexts. These fastening solutions are critical in industries where precision and durability are of the greatest importance, such as automotive, aerospace, and electronics.
Durability and Strength
One of the primary reasons these fasteners are used in industrial design is their incredible durability. Made from strong materials like stainless steel, carbon steel, and titanium, these components are built to endure harsh conditions. These include exposure to extreme temperatures, high pressure, and constant vibration—situations commonly found in industrial settings.
The strength of these fasteners is essential for maintaining the long-term integrity of the products they help construct. Whether they’re used in heavy machinery or delicate instruments, these components provide a reliable solution that can handle both static and dynamic loads, ensuring the product stays securely assembled.
Precision in Design and Manufacturing
Precision lies at the core of industrial design, and these specialized fasteners are essential for maintaining that accuracy. In applications where every millimeter matters, such as in medical devices or electronics, these components are produced with tight tolerances. This ensures they fit perfectly into pre-tapped holes, providing a secure hold without causing damage to the surrounding materials.
Their precision makes these fasteners ideal for high-performance tasks. For example, in the aerospace industry, even a minor error in fastening could lead to catastrophic consequences. Machine head screws offer the accuracy required to guarantee safety and functionality in such demanding environments.
Versatility in Application
These screws are incredibly versatile and are used in a range of industries and products. In construction, they are commonly employed to join metal components, while in electronics, they secure circuit boards and other fragile parts. Their design allows them to be easily tightened or loosened with standard tools, making them a practical solution for both assembly and repair work.
Additionally, these components can be customized to suit specific project requirements. Manufacturers can produce them in a variety of sizes, lengths, and thread pitches, providing flexibility for unique fastening needs. This adaptability makes them the go-to choice for complex or unconventional industrial applications.
Corrosion Resistance
In industrial environments, exposure to moisture, chemicals, and other corrosive substances is common. For this reason, corrosion resistance is a critical factor in selecting the appropriate fasteners. Stainless steel and coated versions are often chosen for applications where rust or corrosion could jeopardize the integrity of the structure.
These corrosion-resistant fasteners are especially important in industries such as marine, where equipment is frequently exposed to saltwater, or chemical processing, where corrosive substances are regularly handled. This feature ensures that the fasteners maintain their strength and functionality over extended periods, even in challenging environments.
Also Read: The Ultimate Guide to Keeping Your Machinery in Top Condition
Impact on Product Longevity
Such fasteners directly contribute to the longevity of the products they hold together. Since they are designed to provide secure and stable connections, they help prevent mechanical failures. This is particularly important in industries where product reliability is critical, such as automotive manufacturing or the production of heavy machinery.
Manufacturers can significantly reduce the need for repairs and replacements by using high-quality fastening solutions. This extends the lifespan of the product and lowers maintenance costs over time. Ultimately, these components play a vital part in ensuring that industrial products are built to withstand the test of time.
Machine head screws may seem like a minor part of industrial design, but their impact is immense. They provide the strength, durability, and precision needed to assemble everything from large machinery to intricate electronic devices. Their versatility and reliability make them indispensable across countless industries. Whether ensuring the safety of an aircraft or securing a complex piece of electronics, these components are truly built to last.