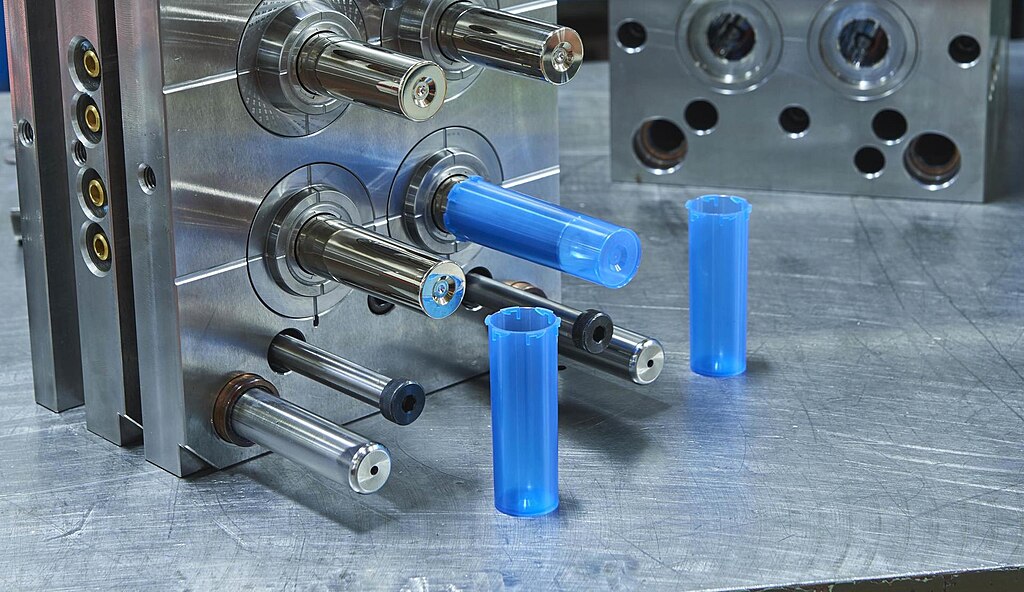
The medical industry continually evolves, with innovations driving improvements in patient care and treatment options. Among these advancements, plastic injection over-molding and insert molding have emerged as critical techniques in producing high-quality, reliable devices.
These processes, offered by Medical plastic injection molding companies, play a crucial role in the safety and effectiveness of healthcare equipment. But what exactly are over-molding and insert-molding, and why are they vital in the medical field?
Understanding Overmolding in Medical Applications
It involves creating a unified component by molding one material over another. This technique combines materials in healthcare applications, each offering specific properties, into one cohesive part. For instance, a rigid plastic base might be over-molded with a softer, more flexible material to create a medical device that is both durable and comfortable for the patient. The process not only improves the functionality of medical devices but also offers increased design flexibility, allowing for the creation of shapes and structures.
Moreover, this process reduces the need for additional assembly steps, as components are molded directly onto each other. This efficiency is critical in this field, where precision and reliability are paramount. Minimizing the number of components and assembly steps is essential for reducing potential failure points, which is vital for ensuring patient safety.
The Significance of Insert Molding in Healthcare Device Production
It is another essential process in the production of advanced devices. This technique involves placing an insert, typically made of metal or another material, into a mold before injecting plastic around it. The result is a single, integrated component combining the properties of the insert and the plastic. This process is precious in creating components requiring metal strength and plastic’s versatility.
In the healthcare industry, this process is often used to produce parts that must be robust and lightweight. For example, surgical instruments and medical devices that must withstand rigorous sterilization processes benefit from the durability of the metal insert. Simultaneously, plastic encapsulation provides a lightweight and manageable device. Achieving this balance of durability and ease of use is essential in medical applications where precision and dependability are paramount.
Enhancing Device Performance
Both processes contribute significantly to the performance of these devices. Combining materials with different properties allows manufacturers to tailor devices to meet specific medical needs. For instance, over-molding can add ergonomic features, such as non-slip grips or soft-touch surfaces, improving the user experience for patients and healthcare providers. Similarly, insert molding can incorporate metal threads or connectors into plastic housings, enhancing the device’s structural integrity.
These processes also enable the production of devices with complex geometries that, if possible, would be difficult to achieve through traditional manufacturing methods. Creating intricate, multi-material components in a single process improves device performance and reduces production costs and time-to-market, making advanced healthcare devices more accessible.
Material Considerations
Choosing suitable materials is crucial in these processes. The materials must not only meet the mechanical requirements of the device but also comply with stringent medical standards. For instance, the materials utilized in these processes must be biocompatible, ensuring they do not trigger adverse reactions upon contact with the human body. Additionally, they must withstand sterilization processes without degrading, ensuring the long-term reliability of these devices.
Furthermore, the compatibility of the over-molded materials or the insert with the plastic is essential for ensuring a strong bond between the components. This bond is critical for the device’s durability and performance, especially in medical applications where failure is not an option. Manufacturers must meticulously choose and evaluate materials to ensure they fulfill all requirements, balancing performance, safety, and regulatory compliance.
Also Read: Innovations in Injection Molding: Crafting High-Performance Solutions
The Value of Partnering with a Professional Company
Working with a professional company offers significant advantages for medical device manufacturers. These companies bring expertise in over-molding and insert molding processes, ensuring that the final products meet the highest quality and safety standards. A professional partner can guide manufacturers through material selection, mold design, and process optimization, all critical for producing reliable devices.
Moreover, a professional company will have the necessary certifications and quality control systems to comply with regulatory requirements. This is particularly important in the medical field, where adherence to strict guidelines is mandatory. By partnering with an experienced company, manufacturers can reduce risks, streamline production, and ensure their devices are ready for market without compromising quality or safety.
These are not just manufacturing processes; they are essential techniques that enable the creation of advanced medical devices. Combining the best properties of different materials enhances these devices’ functionality, reliability, and safety, ultimately contributing to better patient care. The expertise and precision provided by professionals from Medical plastic injection molding companies further ensure that these critical components meet the highest standards. These processes play a crucial role in the ongoing advancements in healthcare technology.